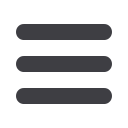
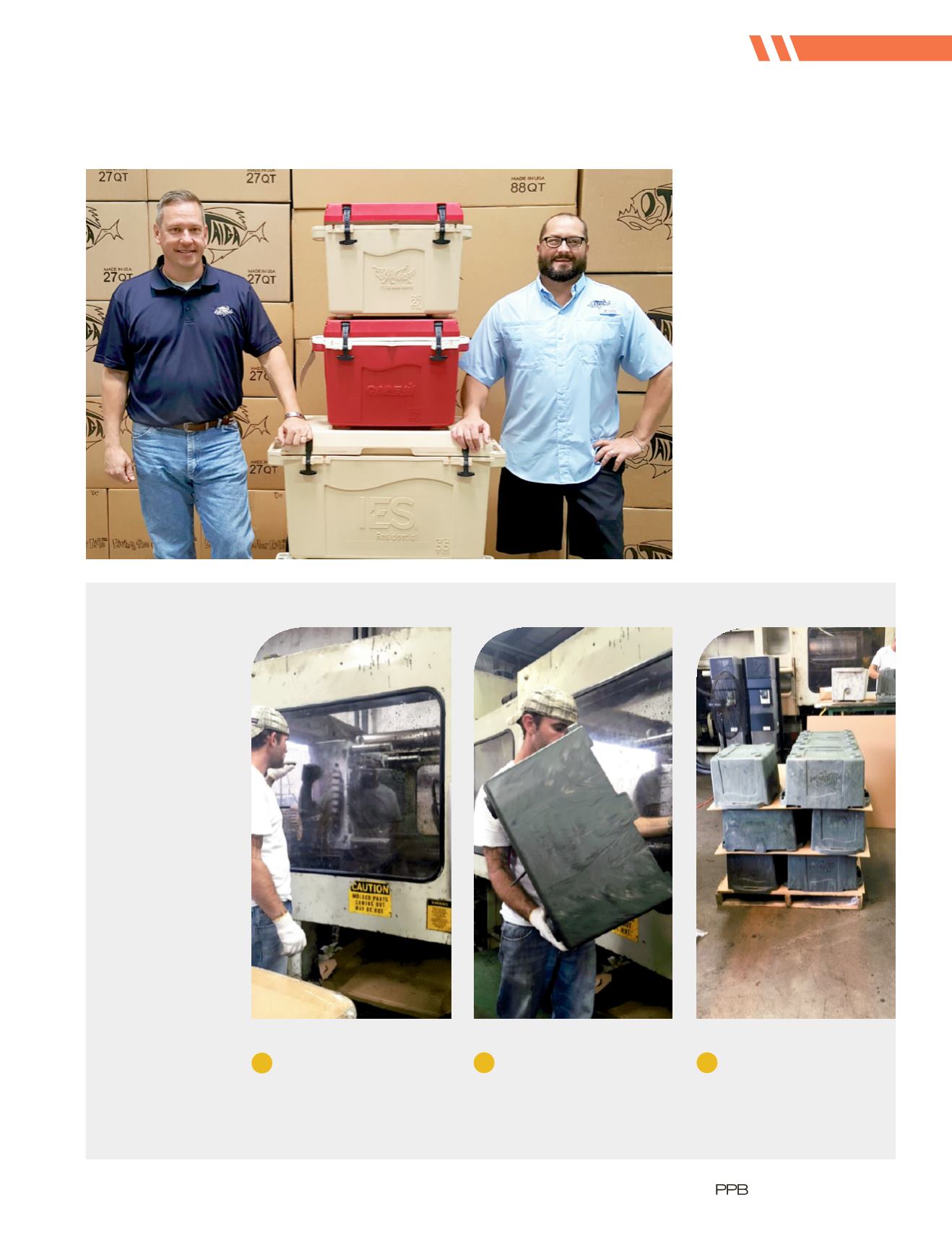
|
DECEMBER 2016
|
109
CONNECT
on the cooler, so the logo is seen
every time a person goes into the
cooler for a beverage.”
The development process—
including the development
and manufacture of injection
molding equipment—took
roughly eight months, says
Hohenshelt. Taiga’s hard-sided
coolers come in standard white
and tan and in camouflage
shades, but the company has
plans to include more styles,
Read on
to learn
how Taiga’s
custom
coolers are
created.
1
A machine operator waits for the
custom injection molding machine to
finish before releasing the cooler.
2
Taiga’s injection molding process
allows for images such as logos and
brand names to be incorporated
directly into the cooler’s plastic shell.
3
Cooler shells bearing Taiga’s
company logo are stacked in
preparation for assembly.
John Hohenshelt, left, and
co-owner Adam Artho are
leaving their mark on the
custom cooler business.