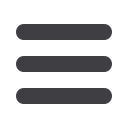
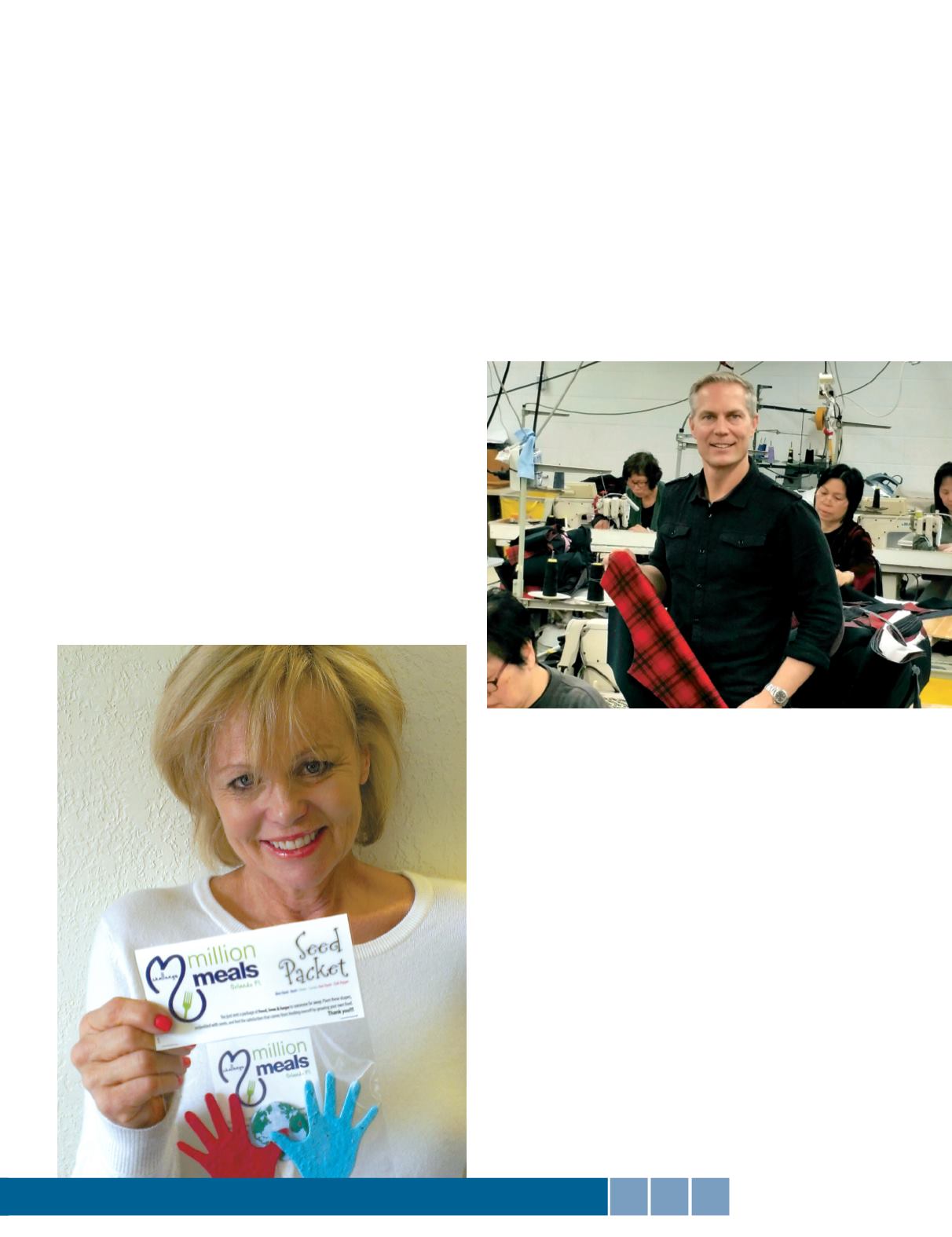
APRIL 2015 •
PPB
• 27
SEEING
GREEN
Sales, still makes the paper one sheet at a time. Over the past
20 years she has worked with thousands of companies who
have purchased her product, and she says the company continu-
ally puts its creative energy into expanding the product line to
appeal to a wider variety of end users. “Some of the largest cor-
porations in the world have used our handmade paper because
it gives them the distinction of showing concern for the envi-
ronment by choosing a recycled, recyclable and biodegradable
product,” she says.
Felson says she has seen the market swing from about 10 to
15 years ago, when companies were using seed paper to “appear
to be environmentally friendly,” to today when it is a priority
and real concern for many corporations. “More and more peo-
ple are looking to go green.” Also, Felson says she is finding
that “Made in the USA” is becoming a label of distinction, as
local manufacturing can be observed and tracked. “All the seeds
we use are from a U.S. supplier. Each batch of seeds we buy
comes with a purity and germination report.”
Creating new and distinctive merchandise is one of their
biggest challenges and at the same time one of their biggest
rewards, Felson says. “Our creativity has always been our
strongest marketing tool. We have been able to produce unique,
one-of-a-kind programs by utilizing product modifications,
changes to the production process and sustainable packaging.”
ECO-RESPONSIBLE AND FASHION FORWARD
Creating fashionable, stylish apparel from recycled plastic
PET (polyethylene teraphthalate) bottles was a visionary idea
when it was launched by supplier Boardroom Eco® Apparel
(UPIC: 214844) in 2001. Since that time, the apparel design
and manufacturing company, located in Vancouver, British
Columbia, which specializes in custom manufacturing, has
introduced low-impact recycled polyester fabrics and closed-
loop apparel recycling.
The company, founded in 1996 by Mark Trotzuk and Lan
Tran, started by offering fashion-forward designs in corporate
promotional apparel and uniforms. Its specialty was researching
the latest fabrics and styles to bring new and exciting apparel
collections to the promotional products industry. But about
eight years ago, Trotzuk, now president, decided to change the
company’s direction.
“Knowing that what I was doing for a living was not that
environmentally friendly, I felt I was going about it the wrong
way.” Instead of manufacturing apparel from traditional fibers,
he created a system that melts pellets made from clean, flaked
plastic water bottles, and then extrudes them into a fiber that
can be processed into fabric for apparel and other items. The
company website states that using the recycled polyester fiber
rather than virgin polyester uses 85 percent less energy and 90
percent less water, and it produces 65 percent less sulfur dioxide
emissions during the process.
To complete the closed-loop process, used garments (100
percent polyester and/or recycled polyester) can be returned to
the company to be recycled into new 100-percent recycled
polyester apparel.
Lauri Felson
Mark Trotzuk