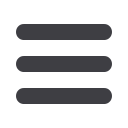
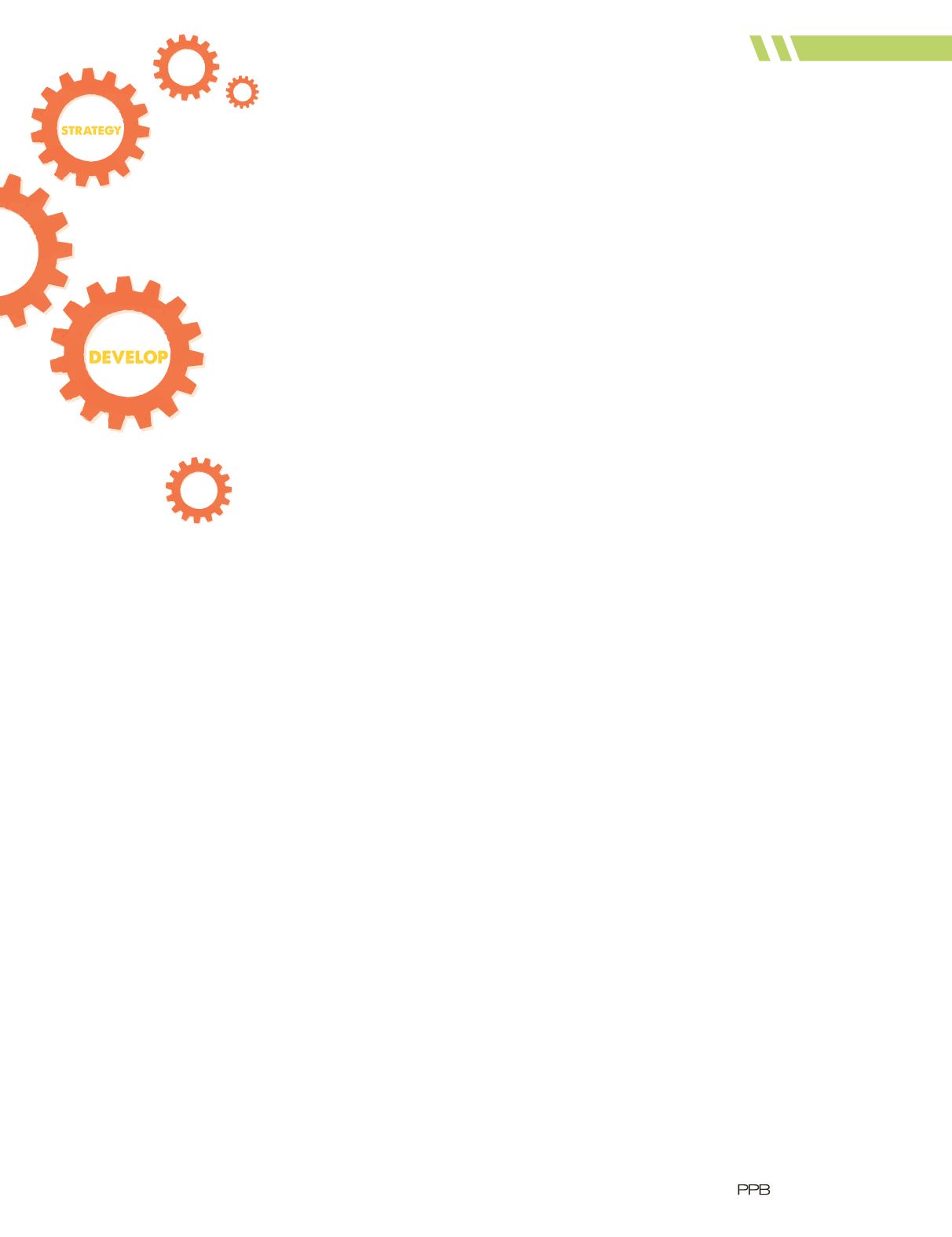
|
JANUARY 2017
|
59
GROW
What Are The QCA
Pillars Of Compliance?
The QCA Compliance
Accreditation Program is
comprised of Five Pillars
of Compliance
©
that
include Product Safety (and
Regulatory Compliance),
Quality, Social Accountability,
Supply Chain Security and
Environmental Stewardship.
Like many compliance
accreditation programs, QCA
employs a proprietary gap
analysis and corrective actions
that are validated by third-party
audit providers. No applicant is
accredited and no member is re-
accredited without completing
the gap analysis, the required
audits and two mock recalls of
products randomly selected from
their line.
The standards against which
QCA audits are performed are:
• ISO-9000 - Product Safety,
Quality and Elements of
Environmental Stewardship
• UN Global Compact Principles
- Social Accountability and
Balance of Environmental
Stewardship (a questionnaire
developed in-house and
benchmarked by Elevate, a
third-party audit provider for
social accountability)
• CTPAT - Supply Chain Security
For more details, download
the QCA Knowledge Series for
free at
http://www.qcalliance.org/knowledge-series
Why Is QCA
A 501(c)(6) Entity?
QCA is categorized by the
IRS as a 501(c)(6) organization.
Our product is education and
information. QCA is subject to
the private inurement doctrine,
which means no benefit may
accrue to any individual member,
nor may unequal standards of
membership be applied. (QCA is
legally obligated to use the same
measuring stick regardless of
company size, name or location.)
Lastly, funding for QCA is based
on dues and fees for service.
Note: QCA does not certify
product or set standards.
An example of a similar board
structure would be PhRMA.
The PhRMA Code pertains to
the design, development and
introduction of new drugs to the
marketplace and the obligation
to educate stakeholders on
the role new medicines play in
patient care. Consistent with this,
a Code revision in 2008 limited
promotional items to only those
with educational value. QCA’s
board, like PhRMA’s, represents
the industry’s leading companies
which are devoted to advancing
the industry and protecting end
users of products.
Do I Need A
Compliance Program?
As a member of the
promotional products industry,
your company is not legally
obligated to adhere to industry
best practice standards. However,
should your product cause
harm to the end user (or violate
U.S. import law), you will want
to have considered the stance
federal regulators have taken:
When you are designing and
manufacturing (or importing)
your product, you should
contact a voluntary standards
organization that may have
standards in place for your
product or for products similar
to yours. Although this is not
a mandatory requirement,
you would be well advised
to consider the guidance
in these other standards
because it is based on the
considered judgment of other
manufacturers, designers and
safety experts.
Consumer Product Safety
Commission (CPSC) “Voluntary
Standards” are available
at
https://www.cpsc.gov/Regulations-Laws--Standards/
Voluntary-Standards/
Voluntary-Standards
The CPSC has consistently
looked to industry best practice
(voluntary) standards when
evaluating culpability for harm
to the consumer, from product
to processes (see Best Buy
Settlement 2016 at https://www.
cpsc.gov/Best-Buy-Agrees-to-
Pay-38-million-civil-penalty.
The settlement included a tested
recall program similar to the
mock recalls performed by QCA
firms as noted above.)
U.S. Customs and Border
Protection is, likewise, poised to
take a more stringent position
(increased fines, embargo and
confiscation) on freight found to
violate import law whether the
product is banned, found to have
been manufactured with forced
and/or child labor or otherwise
violative actions. The State of
California and many promotional
products customers in other
states require certification that the
product was not manufactured
using forced labor.
Takeaway
Compliance programs focus
on detecting, deterring and
Whether
product orprocess,
industry standards
are simply
best practices.