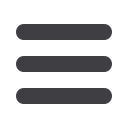
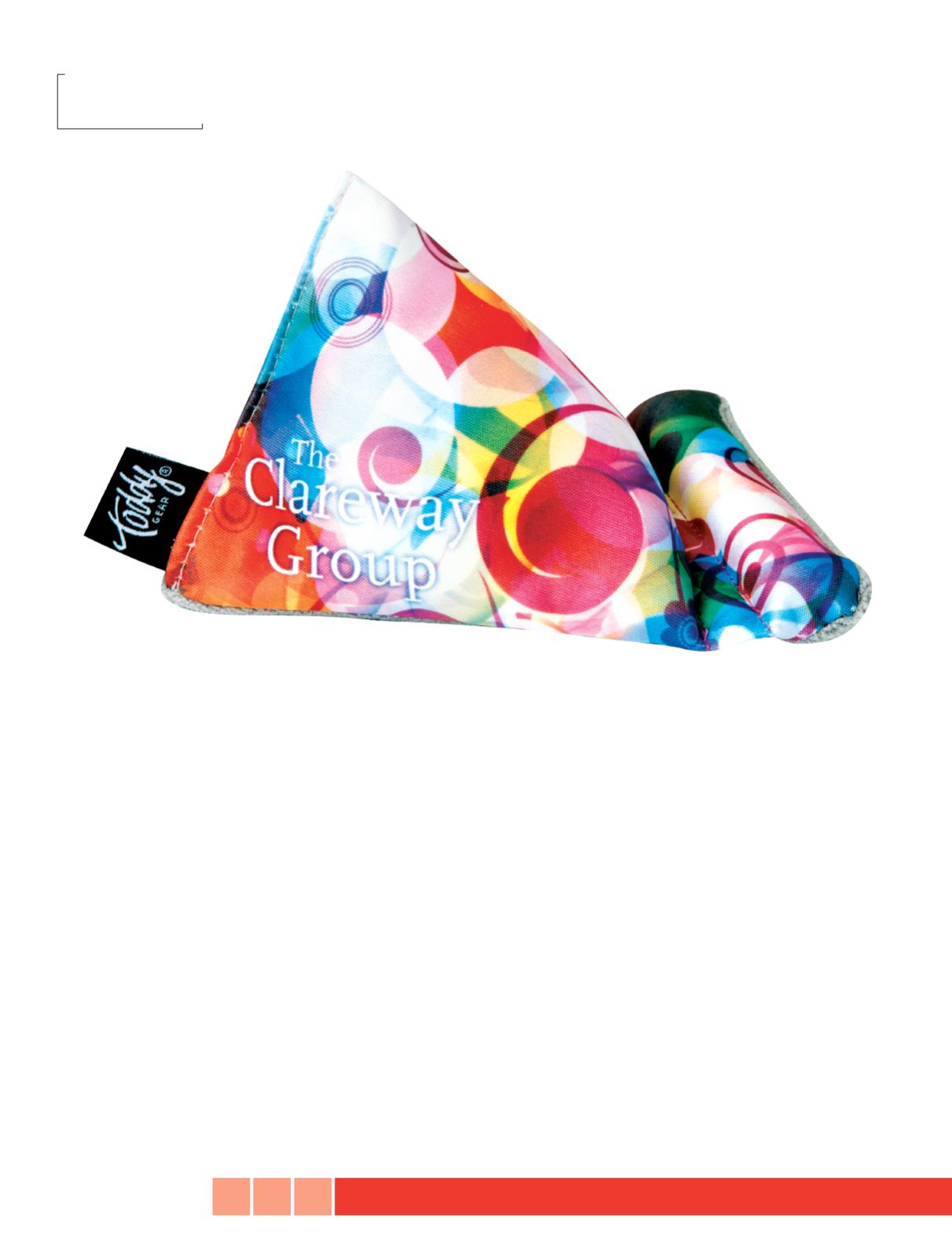
FACTORY FLOOR
“Our simplest item to produce is our Smart Cloth due to its shape and single-
sided imprint,” says Toddy Gear’s Viktorya Kooistro, director of marketing and com-
munications. “Our most complex item is the Stress Ball-Screen Cleaner. It is the
most complex because it is comprised of four individual panels, two of which are
imprinted, and then all of the panels are hand-sewn together.”
TODDY GEAR TURNS OUT FUNCTIONAL MICROFIBER
PRODUCTS FOR TECH DEVICES.
BY JEN ALEXANDER
The production process for Toddy
Gear items requires the majority of
employees involved to have specialized
experience and trade expertise, says
Kooistro. “Positions such as master sew-
ers, digital print operators and press
operators are highly trained in their
trades. For these positions we not only
employ highly-skilled and seasoned pro-
fessionals, we also provide ongoing
training to ensure skill sets are improv-
ing with technology.”
Toddy Gear’s most popular prod-
ucts are its Smart Cloth, the Stress Ball-
Screen Cleaner and The Wedge™
mobile device stand. Read on to learn
how The Wedge is made.
The manufacturing process for The
Wedge begins with Toddy Gear’s art
department reviewing the approved art-
work and optimizing it for print produc-
tion. The print production department
N BOLINGBROOK, ILLINOIS,
supplier Toddy Gear
(UPIC: T516677) is making smooth moves with its
U.S.-made microfiber cloth promotional products. The
company moved its microfiber manufacturing to the
U.S. in 2013, and in its manufacturing facility turns out 13 dif-
ferent types of products, 11 of which are made on-site, while
two non-microfiber items are imprinted at the facility.
I
Clean Sweep
92 •
PPB
• APRIL 2015
CONNECT