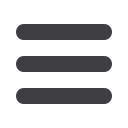
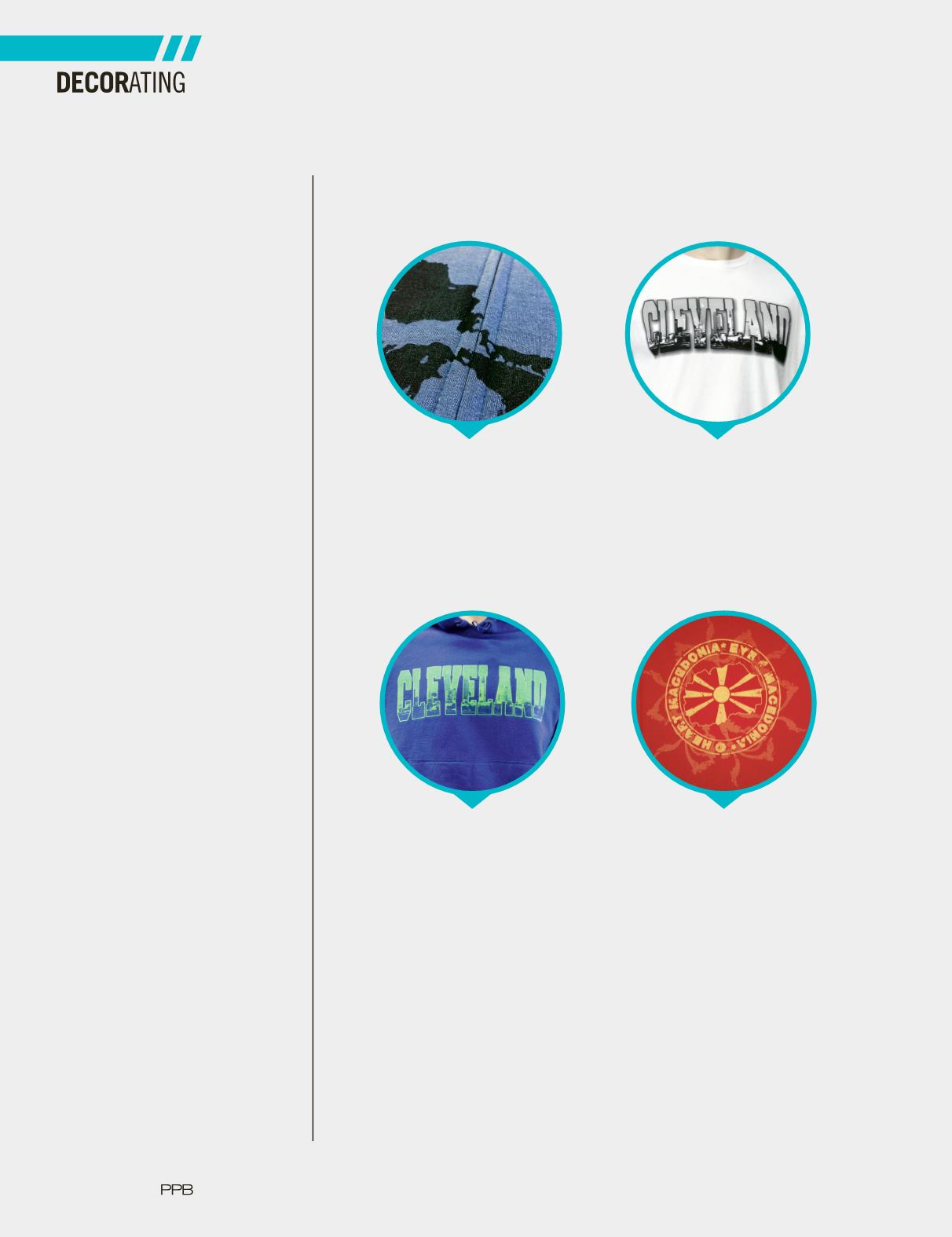
The softness and printability of a
cotton t-shirt greatly depend on
how it’s processed. There are two
primary types of yarn used to make
t-shirts: open end and ring spun. The
difference between the two comes
from the yarn-spinning method.
Open-end cotton yarns typically
use shorter-length cotton fibers and
yield a fabric that has a drier or crisper
hand. Open-end yarns tend to be
coarser, more loosely bound and with
rougher thread.
Ring-spun yarns have longer,
staple-length fibers that require two
steps in the manufacturing process
versus one step used for open-end
yarn. This increases the labor required,
and therefore is one factor in their
higher price.
There are two techniques used to
process yarn: carding and combing.
Carding is just like it sounds: moving
a card over the yarns. It doesn’t really
align the threads, and it doesn’t
eliminate the shorter, roving fibers.
Think of it in terms of combing
your hair with a comb or a card. The
comb is going to sink in and align the
strands so you’ll have a smoother,
cleaner look as opposed to a card that
is just skimming the top. Combing
also breaks the fibers apart, adding to
the softness of the garment.
The gauge or thickness of the yarn
is referred to as “singles.” The higher
the number, the finer the yarn. So, 30
singles is thinner than 20 singles. The
finer the yarns used, the smoother the
surface of the fabric and the softer to
the touch.
An add-on that can enhance the look
of a decorated garment for a nominal
increase in cost is printing over the zipper.
This offers the potential of featuring a
more eye-catching design increasing
the perceived value of the product and
offering greater customer satisfaction.
This design is an example of a discharge
print. When screen printing on dark
colors, a white underbase must be
laid down first as a foundation for the
design. This layer also adds weight to
the ‘hand’ of the shirt. An alternative
process uses discharge inks, which
bleach out the color of the shirt,
leaving a white or neutral area for the
design to be printed on. Because no
underbase is needed, the shirt has a
softer hand. In quantities between 48
and 200 pieces, discharge printing can
lower the overall cost of the product.
Through the use of halftones, it’s
possible to create gradients of the same
color, giving the print a multicolor look
while still only using one color. As each
color costs more when screen printing,
this is a low-cost way to create a more
eye-catching design.
This garment uses several techniques
to lower the cost while increasing the
attractiveness of the overall design.
Using a distressed effect eliminates
the need for a white underbase, which
would normally add to the cost of the
print and create a heavier ‘hand.’
The process also allows for a thinner
deposit of ink, which makes for a
softer-feeling print. Halftones are also
used to create gradients of the single
color, lending a multicolor look without
the cost of additional screens.
What Makes
One T-Shirt
BetterThan
Another?
Four Low-Cost Decorating Ideas
Photos provided by Blue Moon Promotional
22
|
JUNE 2017
|
INNOVATE