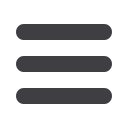
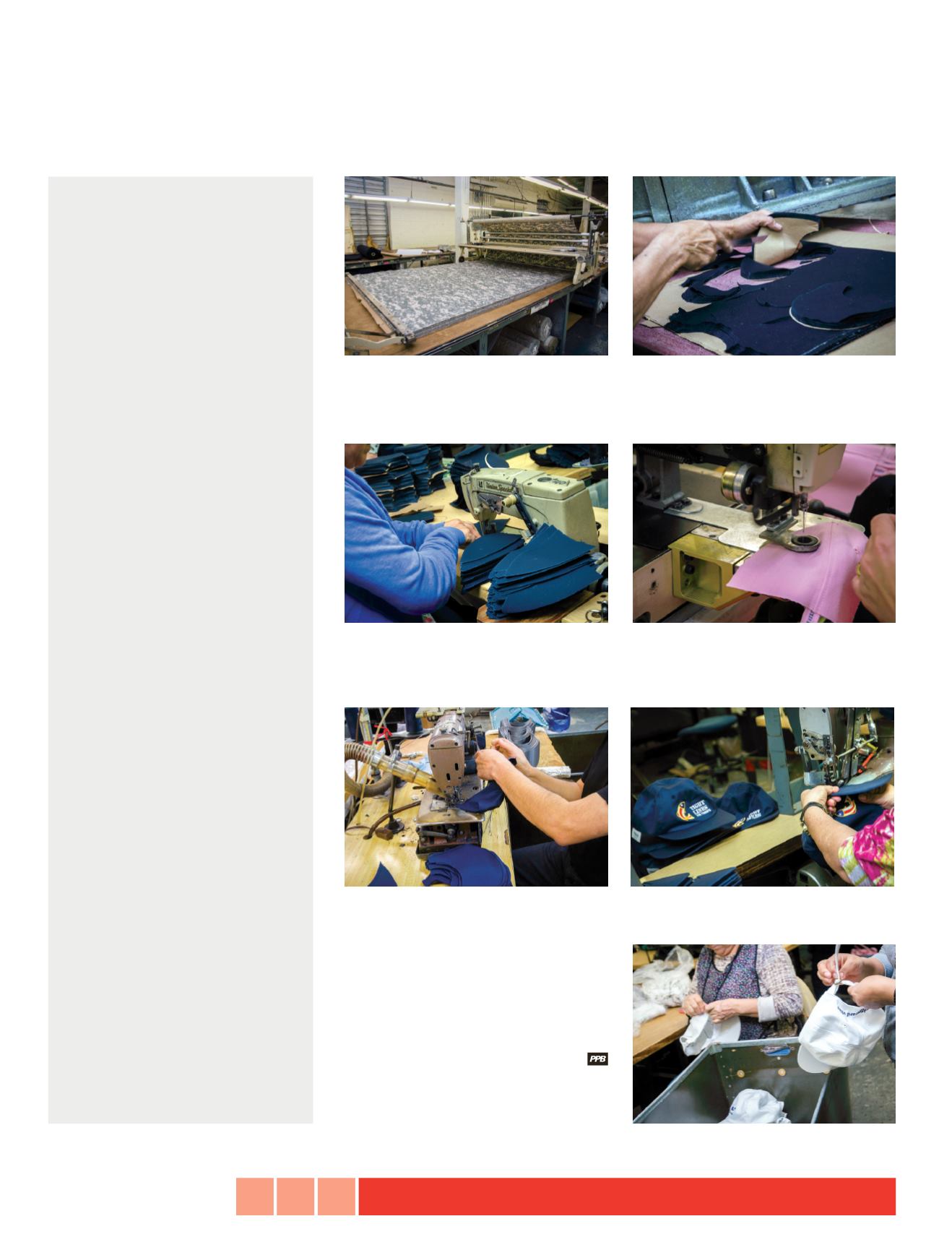
ABOUT UNIONWEAR
Founding date
1992
Principal
Mitch Cahn
Number of orders filled
per year
5,000
Number of employees
140
Size of production facility
70,000 square feet
140 sewing machine operators
Dedicated production lines
Baseball caps
Promotional tote bags
High-end tote bags
Military packs
Bucket and boonie hats
Patrol caps
Duffels, attachés, messenger
bags and backpacks
Types of specialized equipment
Hat taping machine
Robotic blocking unit
Sweatband-making machine
Double-needle hat taping
machine
Bucket-brim stitching machine
Hydraulic die-cutting clicker
Tajima embroidery machines
AS Technologies roll fuser
Zipper
Automated web-cutting
machinery
Programmable tackers
Programmable box stitchers
Roll-to-roll zipper-to-gusset
attach
Self handle machinery
Roll slitter for making handles
The caps begin as a roll of fabric, which is drawn out and cut for the quantity needed per
order. Each panel of the cap is then die-cut according to the type of cap it will be—struc-
tured, unstructured and fitted are a few styles Unionwear makes.
88 •
PPB
• DECEMBER 2015
CONNECT
our facility,” says Bronson.
“Our experience in making both hats and
bags has benefitted the production of both
products,” he adds. “In addition, we have
become experts in decorating unfinished hat
and bag parts, which enables us to get much
better quality, larger embroidery fields and
lower prices.”
Read on to see how Unionwear pieces
together its popular line of hats.
Jen Alexander is associate editor for
PPB.
Visors are produced and attached to the crowns of each cap. Next, the trimming, cleaning
and quality-control process begins.
Finished products are inspected again
before being polybagged, boxed and
shipped.
At sub-assembly stations, the panels are sewn together and eyelets are sewn in as well.
Embroidery is done at the flat-panel stage, as on this back panel. More than 100 embroi-
dery machines run daily at Unionwear.