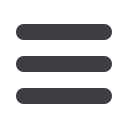
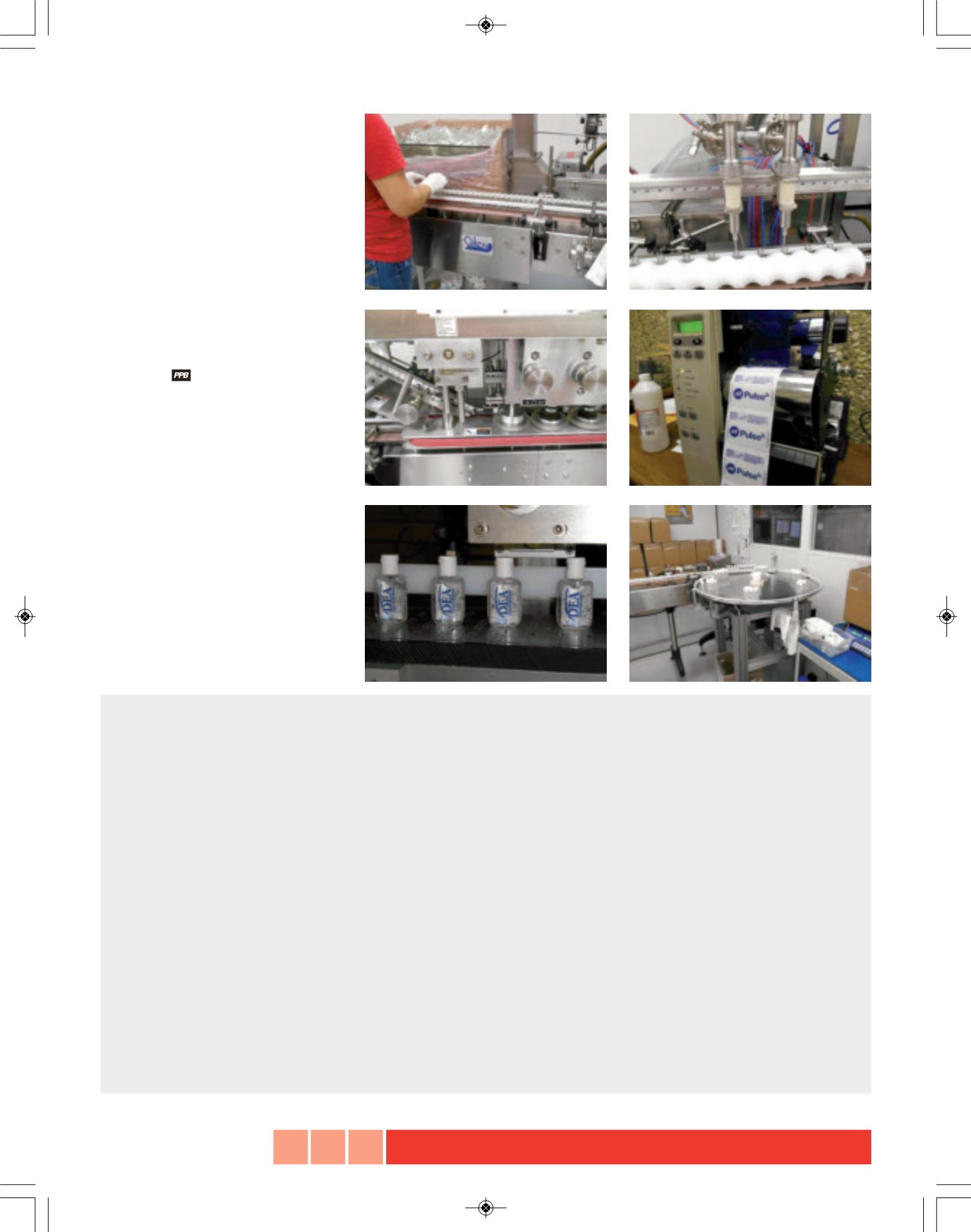
packing, and then they are stored in the
warehouse, waiting for an order.
“When the order comes in, the art is
transmitted electronically from our art depart-
ment to the label printer, and the next thing
we see is a printed, pressure-sensitive label,
ready to apply to the bottle,” Ellis explains.
“We simultaneously apply the ingredients
statement required by the FDA to the back of
the bottle and the customer art to the front.”
Then, the filled and labeled bottle goes
down a conveyor belt for final inspection, and
one more turn of the cap to ensure it’s on
tight, before the product is dropped in a box
for shipping.
Jen Alexander is an associate editor for
PPB
.
ABOUT HUMPHREYLINE
Founding date
1957
Principals
Bitsy and Mel Ellis
Size of production facility
55,000 square feet
Number of employees
54
Types of specialized equipment
Injection molding;
blow molding; silkscreen printing; pad printing; offset
printing; filling lines for the personal care amenities
line; label making; label printing
Special training is needed to operate any equip-
ment in the plant, and floor supervisors and managers
provide the primary hands-on training. Specialized cer-
tification is required for operating equipment, such as
a forklift truck, and for shipping hand sanitizer, which is
classified as a hazardous material if shipped by air. In
addition, HumphreyLine’s Standard Operating
Procedures (SOP) cover nearly every step in manufac-
turing. In order for an employee to be considered
“trained,” he or she must learn the SOP, take a written
test and agree in writing to follow the SOP.
Number of orders filled per year
20,000
Most popular items
Hand sanitizers, stadium cups and
lip balms
The easiest item to make? The egg flat, used in the
commercial egg industry. It requires no decoration, but
is merely molded and shipped. The most complex? Sand
pails and yo-yos. The steps include molding, decorating
and assembling each piece, all to order for custom color
and decoration options. “Any time you have multiple
manufacturing steps, the complexity rises dramatically—
as does the chance for problems,” says Ellis.
Notable accomplishments
This year marked
HumphreyLine’s 20th consecutive year of shipping more
than 99 percent of its orders complete and on time.
TOP LEFT
A HumphreyLine employee places
empty bottles on the filling line.
TOP RIGHT
Gel sanitizer is dispensed from two nozzles,
each loading 1/4 ounce, into half- ounce bot-
tles.
MIDDLE LEFT
The automatic capper
applies the cap to the top threads of the
filled bottles.
MIDDLE RIGHT
Printed labels
are ready to apply to sanitizer bottles.
BOT-
TOM LEFT
Labeled bottles of hand sanitizer
glide down the belt at HumphreyLine’s fac-
tory, ready to keep end users healthy.
BOT-
TOM RIGHT
Samples are tested to ensure
the product meets quality standards.
82 •
PPB
• DECEMBER 2014
CONNECT
201412_FactoryFloor_PPB 2013 11/14/14 9:09 AM Page 82